膠輥硫化罐是膠輥生產(chǎn)中的核心設(shè)備,其工作原理和工藝優(yōu)化直接影響膠輥的質(zhì)量和生產(chǎn)效率。以下詳細(xì)介紹膠輥硫化罐的工作原理和優(yōu)化硫化工藝的方法:
一、膠輥硫化罐工作原理
膠輥硫化罐通過提供高溫高壓環(huán)境,促進(jìn)橡膠分子交聯(lián),使膠料從塑性狀態(tài)轉(zhuǎn)變?yōu)閺椥誀顟B(tài),從而獲得所需的物理性能和化學(xué)穩(wěn)定性。
加熱系統(tǒng): 通常采用蒸汽、電加熱或熱油加熱,提供硫化所需的熱量。
壓力系統(tǒng): 通過壓縮空氣或氮氣提供壓力,促進(jìn)膠料流動和填充,提高膠輥密度。
控制系統(tǒng): 采用PLC或DCS系統(tǒng),控制溫度、壓力和時間等參數(shù),實現(xiàn)硫化過程的自動化。
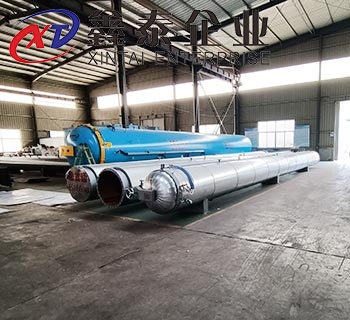
二、優(yōu)化硫化工藝的方法
確定合適的硫化參數(shù):
硫化溫度: 根據(jù)膠料種類和性能要求確定,溫度過高會導(dǎo)致過硫,過低則會導(dǎo)致欠硫。
硫化壓力: 根據(jù)膠輥規(guī)格和膠料流動性確定,壓力過高會導(dǎo)致膠料流失,過低則會導(dǎo)致膠輥密度不足。
硫化時間: 根據(jù)硫化溫度和膠料厚度確定,時間過長會導(dǎo)致過硫,過短則會導(dǎo)致欠硫。
優(yōu)化硫化過程:
分段硫化: 采用不同的溫度和時間進(jìn)行分段硫化,提高硫化均勻性和效率。
預(yù)硫化: 在成型后進(jìn)行預(yù)硫化,提高膠料強度,減少正式硫化時間。
后硫化: 在正式硫化后進(jìn)行后硫化,進(jìn)一步提高膠輥性能。
改進(jìn)硫化設(shè)備:
采用高效加熱系統(tǒng): 如微波加熱、遠(yuǎn)紅外加熱等,提高加熱效率,縮短硫化時間。
優(yōu)化壓力控制系統(tǒng): 采用變頻控制技術(shù),實現(xiàn)壓力的精確控制。
升級控制系統(tǒng): 采用智能控制系統(tǒng),實現(xiàn)硫化過程的自動化控制和數(shù)據(jù)記錄。
總結(jié):
了解膠輥硫化罐的工作原理,并采取有效的優(yōu)化措施,可以顯著提升膠輥硫化質(zhì)量和生產(chǎn)效率。企業(yè)應(yīng)重視硫化工藝的優(yōu)化,不斷探索新技術(shù)和新方法,以提高產(chǎn)品質(zhì)量和市場競爭力。